Closed factories, clogged ports, no truck drivers — up and down the global supply chain there are problems, raising concerns that it could disrupt the global economic recovery.
So what’s behind the issue?
Raw material shortages
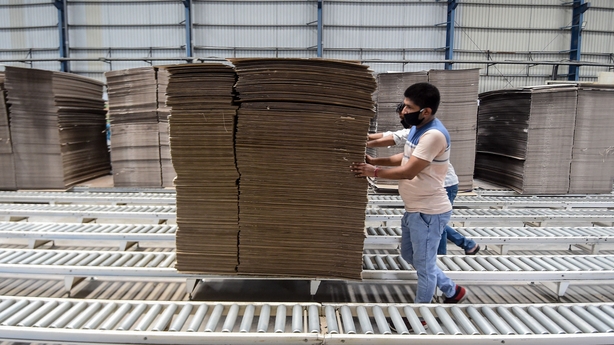
Developing countries have faced a sudden surge in demand for their raw materials as economies reopen and recover from the Covid pandemic.
“Raw materials still come mainly from emerging nations such as India and Brazil where the management of the pandemic is complicated,” said Isabelle Mejean, an economist and professor at Sciences Po university in Paris.
With people working from home and shopping online, demand for cardboard to deliver packages has surged.
Both the construction and furniture industries have also seen booms in demand as those stuck at home want to improve their living space, with giants like Ikea having trouble keeping items in stock.
The competition for wood has caused shortages for book publishers.
Another problem can be the high concentration of firms that transform raw materials for use by manufacturers. For example, the closure over the summer of a US factory that makes specialised plastics for the perfume industry caused headaches for the entire industry.
Even where it is possible for manufacturers to substitute certain materials, it requires adjustments in factories, said Yann De Feraudy, deputy CEO for operations at cosmetics firm Yves Rocher and head of the France Supply Chain trade association.
If you can’t do that, “you have to order three months in advance … Prices rise until there is nothing” left available.
Factories at a standstill
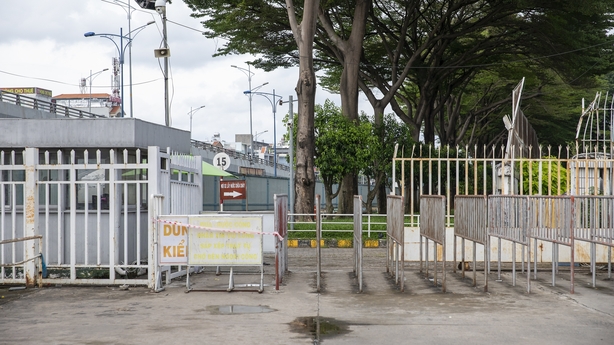
The pandemic has demonstrated the dependence of the world on factories in Southeast Asia, said Jonathan Owens, a logistics specialist at the Salford Business School in Britain.
He calls for some manufacturing to return to the West to reduce the dependence on one region.
“So where the raw products might still come from the Far East, the assembly might be actually manufactured in different regions of the world and then it’s distributed,” he said.
Covid clusters and lockdowns have resulted in the closure of some factories, such as textile and shoe factories in Vietnam that are causing trouble for big brands such as Nike and Adidas.
For components like semiconductors, factory closures at chip factories have caused an avalanche of problems.
A lack of processors has forced carmakers to idle their factories and is set to cause the industry $210 billion in losses this year, according to consulting firm Alix Partners.
And Covid-19 is not the only reason for disruptions: There have also been cyberattacks and natural disasters, along with power cuts in major exporter China.
Blocked ports, lack of containers
Ports have had trouble handling the surge in goods shipped, as well as disruptions.
A container ship blocked Egypt’s Suez Canal, a vital maritime shortcut, for only six days but it caused a backup in traffic that taxed the capacity of European ports.
“After the Suez Canal blockage, it took two months for the small European ports to settle down,” said Owens.
Another disruption was caused by the two-week closure of the Chinese port of Ningbo-Zhoushan, the world’s third-largest in terms of exports.
“Freight containers that should be in Egypt right now, they’re actually stuck in China,” said Owens.
The main port on the US West coast at Los Angeles has had dozens of ships waiting to unload their containers, and will now work 24 hours a day in an attempt clear the backlog.
All the disruptions have led containers not being in the right place.
Shipping costs have jumped by a factor of 10 over the past year-and-a-half.
Lack of drivers
Increased customs checks following Britain’s exit from the European Union have caused problems in the country, which is also suffering from a shortage of truck drivers as many came from EU countries.
The British government has offered short-term visas to try to help ease the shortage, which other countries also confront to a lesser extent.